
Han X, Yang D, Yang C, Spintzyk S, Scheideler L, Li P, Li D, Geis-Gerstorfer J, Rupp F (2019) Carbon fiber reinforced PEEK composites based on 3D-printing technology for orthopedic and dental applications. Phys Procedia 56:147–156Įlhattab K, Hefzy MS, Hanf Z, Crosby B, Enders A, Smiczek T, Haghshenas M, Jahadakbar A, Elahinia M (2021) Biomechanics of additively manufactured metallic scaffolds-a review. CIRP Ann 56(1):205–208īourell DL, Watt TJ, Leigh DK, Fulcher B (2014) Performance limitations in polymer laser sintering. Schmidt M, Pohle D, Rechtenwald T (2007) Selective laser sintering of PEEK. Mater Lett 263:127227īerman B (2012) 3-D printing: the new industrial revolution. Biomaterials 28(32):4845–4869Įlhattab K, Sikder P, Walker JM, Bottino MC, Bhaduri SB (2020) Fabrication and evaluation of 3-D printed PEEK scaffolds containing Macropores by design.

Kurtz SM, Devine JN (2007) PEEK biomaterials in trauma, orthopedic, and spinal implants. Panayotov IV, Orti V, Cuisinier F, Yachouh J (2016) Polyetheretherketone (PEEK) for medical applications. Park SJ, Lee JE, Park J, Lee N-K, Son Y, Park S-H (2021) High-temperature 3D printing of polyetheretherketone products: perspective on industrial manufacturing applications of super engineering plastics. CRC Press, Engineering thermoplastics, pp 299–314 This paper confirms that high-quality PEEK-based filaments can be developed in-house to yield 3D-printed PEEK parts with optimum mechanical properties. The highest mean strengths recorded for the parts printed with the LD filaments were 106.45 MPa (compressive), 85.43 MPa (tensile), and 102.63 MPa (flexural). Notably, results confirmed no significant differences between the specimen groups developed using LD and CA filaments, highlighting that the LD filaments were of comparable quality to the CA ones. Results indicate that an optimum combination of a nozzle and chamber temperature, print speed, and layer height is appropriate to achieve 3D-printed parts with optimum mechanical properties.
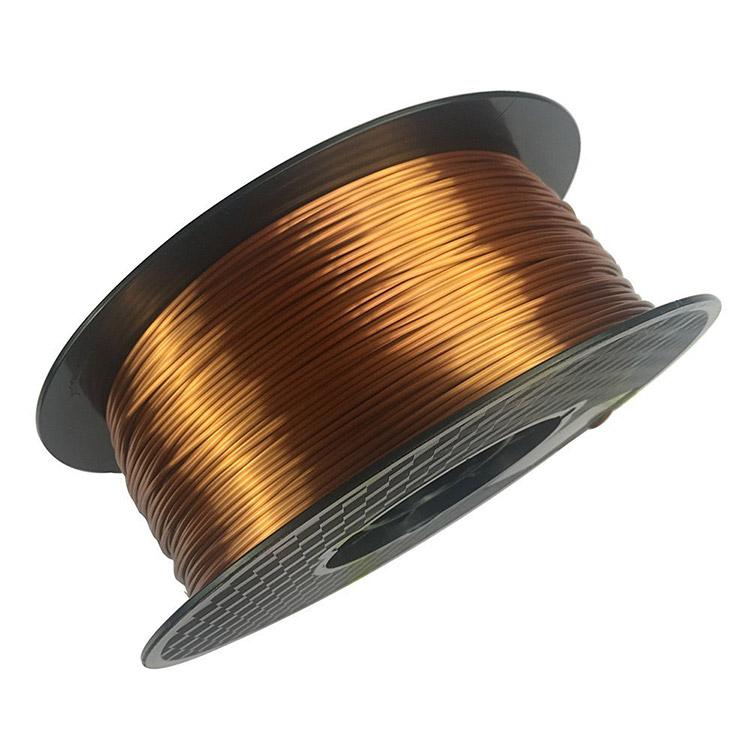
In that regard, we developed PEEK filaments using a customized extruder setup in-house and used those laboratory-developed filaments (LD) to 3D print PEEK structures suitable for mechanical testing (tensile, compression, and flexural testing) and compared them to the mechanical properties of 3D-printed parts that were developed using commercially available (CA) filaments. Moreover, we explore the effect of filament quality on the structures’ mechanical properties. In this paper, we investigate the effect of specific 3D printing parameters such as nozzle and chamber temperature, print speed, and layer height on the mechanical properties of 3D-printed PEEK. Indeed, it is critical to consider specific 3D printing parameters and filament feedstock quality to achieve optimum mechanical properties in the 3D-printed PEEK parts. 3D printing, specifically fused deposition modeling (FDM) of poly-ether-ether-ketone (PEEK), is one of the most powerful and efficient state-of-the-art manufacturing techniques.
